I decided I wanted to try making some punch tooling in order to manufacture a couple of the parts involved in a traditional concertina action: the felt washers that go under the buttons and the leather grommets that screw onto the ends of the action levers.
As well as the big Smart & Brown 2-ton toggle press mentioned previously, I also have a little 600N Brauer one (if my calculations are correct, the big one is rated to deliver about 30 times the force of the little one). I got it second hand some time ago, with some odd custom tooling attached to it that I never figured out what it was supposed to do. Here it is after removing the tooling and cleaning it up a little (yes, that is an old gear knob on the end of the handle – actually quite a nice addition so I left it on):
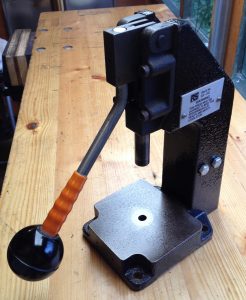
Because the throat height of the press is considerably more than the thickness of a piece of felt or leather, I turned up a 50mm tall spacer block from scrap 1″ mild steel bar. It bolts to the table of the press and has an M8 threaded hole in the top for the punch anvil, and a cross hole for the ejection of waste punched through the hole in the middle of the anvil.
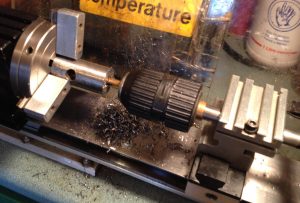
I needed to cleanly bore out the inside of the felt washer punch, so I ground a simple D bit from the 1/4″ shank of a broken HSS end mill:
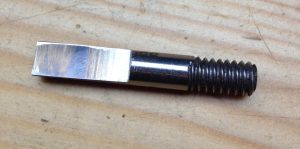
I drilled most of the waste out first, then used the D bit to open it out to 1/4″ and cut a flat bottom on the hole. At this stage I also drilled a 1.5mm hole for the centre pin:
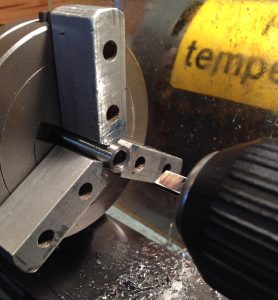
I used the compound slide to turn the tapered sections of the top punches, stopping while the edge was still fairly blunt. After hardening and tempering, I put them back in the lathe and used emery paper to clean up the taper and sharpen the edge.
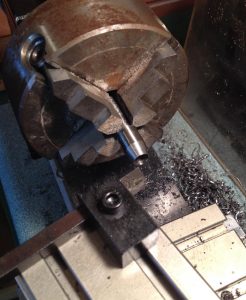
Threading the other end of a punch with an M8 die so it can screw into the press arbor:

The anvil and felt washer punch installed in the press. I made the half-nuts that are used to lock the tool at the desired height by facing ordinary full nuts on an arbor.
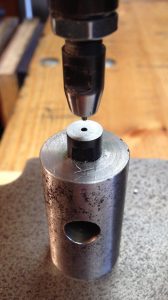
Here’s a quick video clip showing the felt washer punch in use:
This shows where the washers go on the buttons, to stop them making a clacking noise when they bottom out:
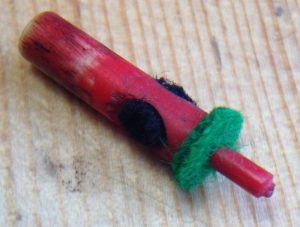
A nice stockpile of washers for my first few instruments. I made these from a sample piece of ‘baize’ woven wool cloth as used on gaming tables. I also have several other sample pieces in various different colours. I think the original washers may have been made from an actual fine, thin felt rather than a woven cloth, though – I need to get hold of some samples to experiment with.
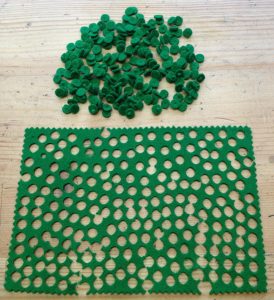
The first anvil I made had a design flaw: the hole through the middle for the ejection of waste material was drilled 1.5mm diameter all the way through the tool. In practise it quickly became constipated and I had to repeatedly remove it and drill out the waste. The one on the right is a second, improved version that is relieved to a larger diameter until a couple of mm from the top surface:
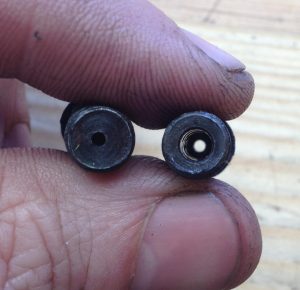
Here are all the punches and anvils I made. The first one is the felt washer punch. Inside it is a couple of layers of spongy foam and then a couple of felt washers; with careful adjustment of the pressing force this seems to be just right to prevent the washers getting stuck inside. The second one I had optimistically hoped might work the same way, but the grommets just got stuck inside it and wouldn’t come out, so I instead decided to use it to punch out the centre hole and mark the location of the outside of the grommet, then switch to the third punch which has a slot milled in the side to allow the grommets to be pushed through and removed from the top.
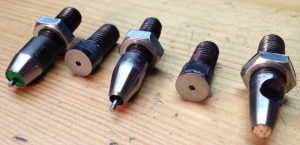
Here is a video clip showing the leather grommet punches in use. Note that in the video I was using 2.5mm veg tan cowskin, however I subsequently found that I got much better results from 4mm leather instead (the 2.5mm leather compressed down to 1.5mm in the punching process and the 4mm to about 3.2mm). I also removed the stripper plate seen in the video because I found it was getting in the way and causing more trouble than it was worth:
This shows where the leather grommets go inside the instrument. They screw onto the end of the lever arm (which is lightly threaded), then glue to the samper disc on top of the pad:
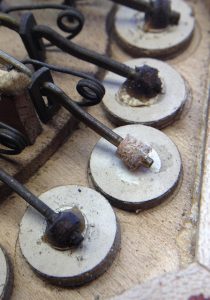
A couple of hundred leather grommets for my first few instruments:
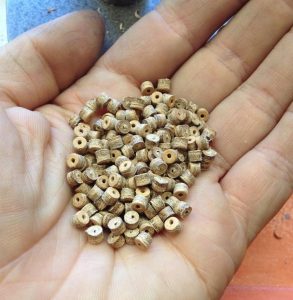
Although these are fairly trivial parts, it certainly feels like progress to be stockpiling significant quantities of production-quality parts that I have made using my own tooling.
UPDATE: I’ve since got hold of some 0.8mm piano bushing cloth and punched more washers from it:
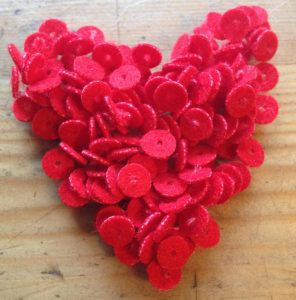
The piano bushing cloth is thinner, finer, and more tightly woven than the baize. Unfortunately I’ve only been able to find it in bright red with a white core. I may experiment with dyeing some of it black.